Condition Monitoring Specialist at AB InBev
Job Overview
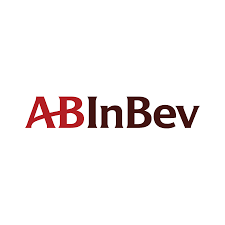
Condition Monitoring Specialist at AB InBev
Condition Monitoring Specialist at AB InBev
AB InBev
Dar es Salaam
Dreaming big is in our DNA. It’s who we are as a company. It’s our culture. It’s our heritage. And more than ever, it’s our future. A future where we’re always looking forward. Always serving up new ways to meet life’s moments. A future where we keep dreaming bigger. We look for people with passion, talent, and curiosity, and provide them with the teammates, resources and opportunities to unleash their full potential. The power we create together – when we combine your strengths with ours – is unstoppable. Are you ready to join a team that dreams as big as you do?
The key purpose of this role is to ensure optimal asset performance through loss elimination, risk management, life cycle management and identification, implementation and entrenchment of best practice. To ensure efficient management of the fixed cost maintenance plan for the asset.
Key roles and responsibilities
Condition Monitoring Techniques:
Develop and manage Plant footprint to ensure the correct condition monitoring techniques are applied in order to prevent functional failures
Apply RCM practices to prevent functional failures (Vibration Spectrum
Analyses, Oil Analyses, Thermography, Ultrasonic Analyses)
Monitor to detect the onset of deterioration and provide a measure of the extent and rate of deterioration
Incorporate condition monitoring techniques into SIC systems
Maximize asset reliability and availability:
Deliver JIT approach to maintain assets in Plants according to Condition Monitoring results
Continually review and optimize predictive maintenance plans to ensure maximum output at minimum cost
Identify trends in asset performance using RCM analysis and implement solutions to reduce breakdowns and improve machine efficiency by
Applying predictive maintenance solutions
Analyze asset performance trends to generate and support preventative and predictive improvement plans
Monitor reliability indicators based on the condition monitoring report, failure reports and notifications generated
Monitor adherence to the preventative and predictive maintenance plans; adjust accordingly and take corrective action
Monitor assets, condition monitoring indicators and take necessary corrective actions
Prevention of functional failures and avoid the consequences of functional failures
Drive the resolution of failures through structured problem solving:
Evaluate effectiveness of Regional problem solving through the analysis of formal problem solving documentation
Facilitate higher level problem solving for assets by applying standard problem solving tools –informed by Loss & Waste and Condition Monitoring analyses
Risk and life cycle management of assets:
Identify maintenance risks and address accordingly by applying the correct condition monitoring techniques
Maintain the maintenance TCO and ensure appropriately prioritized plans to extend equipment life
Optimize the asset maintenance life cycle cost through life cycle costing analysis
Reduce life cycle costing by improving asset maintainability
Identify, implement and entrench best practice:
Implement condition monitoring best practice
Where best practice is not available, identify and define good condition monitoring practices (benchmarking against similar assets where possible) and implement accordingly
Identify and eliminate poor maintenance practices
Ensure adherence to internal and external condition monitoring standards
Drive efficiency by ensuring that learnings from downtime and condition monitoring findings are replicated across similar asset across the group
Reduce mean time to repair and secondary breakdowns by ensuring adherence to good engineering and condition monitoring standards
Training and Development:
Train, coach, assess and sign-off MAS’s and PA’s on condition monitoring best practices and standards
Development of technical standards and work instructions
Projects Delivery:
All new equipment must be included on condition monitoring footprint and the correct techniques must be applied on assets
Incorporate all new equipment into the Condition Monitoring Footprint
Apply correct techniques on assets
Profile
National Diploma (N6) in Engineering or Maintenance Diploma
Ideally 3 years’ experience packaging production experience and/or VISA Level 2
Sound understanding of packaging
Experience in the packaging/utilities environment
Management experience will be advantageous
SAP PM knowledge
Excellent Excel skills
Excellent PC Skills
Superior decision making capability
Strong analytical capabilities and excellent problem solving skills
Proactive self-starter with high energy levels and a bias for action
High level of self-management
Ability to deliver through others, regardless of reporting structures
Ability to work with people at all levels of the organization across different disciplines
Commercial discipline
Ability to work in a matrix / team environment
Additional information:
Band: VIII
SAB/ABInBev is an equal opportunity employer and all appointments will be made in line with SAB/ABInBev employment equity plan and talent requirements.
How to Apply: