Senior Supervisor – Materials Engineering at Geita Gold Mining Ltd
Job Overview
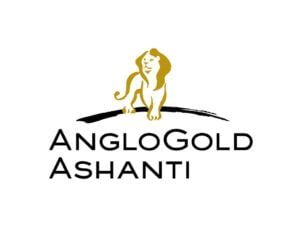
Senior Supervisor – Materials Engineering at Geita Gold Mining Ltd
Senior Supervisor – Materials Engineering at Geita Gold Mining Ltd
Senior Supervisor – Materials Engineering
Location: TZ
ABOUT GEITA GOLD MINING LTD
Geita Gold Mining Ltd (GGML) is Tanzania’s leading gold producer with a single operation in Geita Region. The company is a subsidiary of AngloGold Ashanti, an international gold producer headquartered in South Africa, with operations in more than ten countries, in four continents. The mine is situated in the Lake Victoria Gold fields of Northwestern Tanzania, only about 85 km’s from Mwanza City and 20 km’s Southeast of the nearest point of Lake Victoria. The company has its head office in Geita, only 5 Km’s west of the fast-growing town of Geita, and also a supporting office in Dar es Salaam. Applications are invited from ambitious, energetic and performance driven individuals to fill in vacant position(s) mentioned below:
Position: Senior Supervisor – Materials Engineering
Contract type & Duration: Unspecified Time Contract
Department: Finance & Supply Chain
Reporting to: Superintendent 2 – Materials Engineering
Number of Positions: One (1)
PURPOSE OF THE ROLE:
The role aims to supervise overall of the materials engineering function at site by providing quality control and assurance services to the supply chain department by ensuring goods being purchased are pro-actively well described (cataloguing), cleansed in the Geita Gold Mine limited material management catalogue and assign the right specifications to guarantee that goods are delivered accordingly.
QUALIFICATIONS:
Advanced Diploma or BSC in Mechanical, Electrical, or Automobile engineering.
GGML is an equal opportunity employer: Female candidates are highly encouraged to apply.
EXPERIENCE:
A minimum of six years of working experience in Supply Chain specifically in Materials Management/ Materials Engineering function in the mining environment and other Large-scale companies.
A minimum of 5 years hands on work experience with SAP MM module or any Enterprise Resource Planning (ERP) System/ Cataloguing Application.
MAIN OR KEY ACCOUNTABILITIES:
Lead the team to ensure compliance with GGM environmental, health and safety standard/policies.
Attending to environmental, health and safety related discussions/meetings.
On regular basis, identify/review/flag items for mandatory quality inspection in the catalogue.
Maintain and keep operational a server/network based nonconformance register to record all non-conforming item complaints.
Ensure that soft copies of all reported quality complaints are kept.
Ensure that all reported quality complaints are investigated, and recommendation concluded within three working days from date reported/identified.
On weekly basis, run and share report with respect to outstanding/unresolved quality complaints and advise all stakeholders accordingly.
Attend to technical queries by resolving them within three working days from date reported.
On monthly basis, conduct at least one selective/random quality inspection on identified high potential items, this shall include items with shelf life, types/families with high nonconformance rate, items with higher consumption, fast moving items, etc.
On monthly basis, conduct at least one selective/random quality inspection on identified high potential items, this shall include items with shelf life, types/families with high nonconformance rate, items with higher consumption, fast moving items, etc.
Attend to technical queries by resolving them within three working days from date reported.
On quarterly basis, identify all items which have become redundant/ potential obsolete as a result of parent equipment having been retired, inactive or disposed of and confirm with owners as regards required change (from current status to obsolete) in stock status.
Cause end users to prepare an ANSI to amend stock status as recommended and accepted by end users.
Update the Quarterly Stock Review Register/database with the entire list of items reviewed in the given quarter.
Update/review the offsite repairs register and ensure that all offsite repair purchase requests/ purchase orders are captured as well as information with respect serial number, waybill, quoted repair price, replace cost, etc. are updated.
Cause export documentation to be prepared and items sent for strip & quote not later than seven days from the date of equipment receipt from end user.
Ensure 541 SAP transaction is posted as soon as the component is dispatched to vendor or immediately after purchase order creation.
Ensure quotes/strip-inspection report are immediately reviewed as and when received and advise originators as to whether is worth repairing or not.
Validate replacement price as given by vendor if reflect market price and not inflated.
Monitor vendor performance such that repair quotes are submitted not later than four weeks from date component having been delivery to vendor.
Monitor vendor performance such that repair turnaround time (from purchase order amendment date) is within 6 months for local repairs and within 10 months for international repairs.
Maintain and keep functional a server/network based and system linked Reman Core return and credit claim register, among others showing core reman part number, core description, purchase order number, job number, expiry date, etc.
Identify/chase for core return, update the register with core returns from workshops to Mantrac, and capture/reconcile credit notes receipts from Mantrac.
Maintain, update/review Strategic Spares register and ensure that all Strategic spares are captured and updated.
Ensure, at least once per month, all strategic spares are inspected to determine their physical quantity, physical condition and advise stakeholders accordingly.
Reconcile the ANSI register with the system (SAP) item catalogue, Infinity (catalogue maintenance) system and ensure that all ANSI register entries are reflected in both systems and if not, take appropriate action or advise stakeholders accordingly.
Identify and arrange to code all items which are not in catalogue (free text) but with high/repetitive purchase frequencies.
Undertake Technical Vendor visits & compile reports.
ADDITIONAL REQUIREMENTS:
Good communication skills in Swahili and English language
Ability to read and interpret technical drawings
Analytical skills
Ability to attend/resolve technical queries relating to products specifications on time
High Integrity
Ability to communicate ideas effectively, both orally and in writing
Good team player
Qualification in Materials Management/Supply chain function is an added advantage.
Registration by Procurement and supplies Professionals and Technicians Board (PSPTB) is an added advantage.
Registration by Engineers registration board (ERB) is an added advantage.
MODE OF APPLICATION:
Please apply by clicking APPLY NOW button below
On the portal you will be required to upload your detailed CV, copies of relevant certificates, e- mail and telephone contacts, names, and addresses of three referees. Please do not attach certificates that are not related to the qualifications stated above.
You will also be required to upload a cover / application letter addressed to “Senior Manager Human Resources”, Geita Gold Mining Ltd”. Subject should be “ Senior Supervisor – Materials Engineering’’
Application Link:
If you struggle to apply via the link provided, please head over to our website https://www.geitamine.com/en/people/ or a step-by-step guide on how to apply for jobs on our recruitment portal (SuccessFactors).
You will be required to present original certificates if you are contacted for interviews.
Internal Applicants (those currently employed by AngloGold Ashanti) must have their application letter endorsed by their Head of Department (HOD) or Manager once Removed (MoR).
APPLICATION DEADLINE:
Applications should reach the above on or before 28th July 2023 at 05:30 PM
Only shortlisted candidates will be contacted for interviews.
Requisition ID: 21456
Category: Inventory & Warehousing
Posting Salary: Market Related